Tuesday, February 27, 2007
Hallway Floor, Before & After
This shot is of the back hall / laundry, you can see the vent for the dryer, as well as the propane gas tubing, sticking out of the wall. Notice the waves in the concrete, as it was troweled to a finsih, shy of a finished job, prior to grinding and staining. The second shot looks down the hall in the opposite direction, looking into the Great Room.
This next shot here is of the
Bobby the Terrazzo Guy
The machine itself is called a planetary polisher, that is, the round diamond-embedded grinding disks (five or seven) are also spinning, in an opposite direction than the main blade, to ensure a smooth surface, free of grinder marks. Get it, the small planets (grinding disks), rotate around the main planetary body?
The next step, after his water has evaporated, and the floor is dry again, I begin by applying a first coat of stain with an insect sprayer, the kind you pump up by hand. I leave the stain sit on top of the cement and let it doing it's work, burning it's color into the concrete's DNA. There is no going back and there is no certainty to the color of the final product, it will be what ever it will be, end of story. Isn't it grand - no control at all - absolutely none.
Labels: in process, m. bdrm
Enter the Solar Age
Friday, February 23, 2007
Tile Free
>
It has always been my goal, when building this house, to eliminate the need for any kind of tile, be it ceramic, or terra cotta, or marble; intended for the floor, ceiling, and, yes, even wall tiles are off the project list.
We are using a fairly new technique on our floors, be they in the bedroom, in the hall, in the bathroom, or anywhere at all! We are using a concrete staining system from DECOSUP, an acronym for Decorative [Concrete] Supplies. They are based in Miami, FL. I used their product here in St. Croix, for one really good reason; the concrete stain they manufacture is a low acidic product, compared to Acid Based Stains, which contain hydrochloric and / or sulphuric. It should come as no surprise that acid is a hazardous material, therefore, read: HAZMAT shipping costs, which are prohibitively costly, especially overseas!
Wednesday, February 21, 2007
In The Weeds
I use the metaphor thus: Toying with concrete for the first time (read: every time is different) is a lot like learning to play golf. At first, one tends to hit a lot of balls into the rough, the high grass, off the fairway, into the sand traps, or, as they in the business, hittin' 'em in the weeds. Maybe this is the most frustrating thing you've ever done in life, that is, constantly putting your golf ball in a place where it is extremely difficult to hit it from, from amongst and under the trees, from deep grass, from under a bush, etc. That being said, I've been in the weeds A LOT.
There is an upside to the predicament, and that is that, besides learning not to hit the ball into the woods, one can also learn how to make some unbelievable shots that wouldn't otherwise be a part of a normal practice regimen. It's no fun being in the weeds, but when you find yourself there, you deal with it. Afterall, some of the craziest things come from learning by burning. So, you spill a little sealer in the new concrete, because the concrete is sealed, the spots show everywhere, what to do?
The first shot here is of the south bedroom in The West Wing, or the blue room. The floor is scored and ready for sealing, which I will do later today. The next three shots are of the guest bathroom floor, which you see here. The border of the room, about 7" wide and which will be stained later, is masked off from the rest of the room. This is after the acid staining and the use of a wire brush to work the stain into the concrete. The finished product will be the emerald green I wanted, with a light aqua, a little darker shade than the master bedroom as the border color. The seams will be filled with white grout, which will really finish the look of ancient stone.
Saturday, February 17, 2007
Floor Scored & Several Days Ago
The top coat of concrete, poured on an average 3/4" to 1" thickness, is white cement. That is, white Portland Cement, instead of the normal shade of gray; the product we used was actually a product of Denmark. Interesting, considering the Danes owned and ran the plantations on these United States Virgin Islands, until the good ole USA bought them prior to WWI, to protect the Panama Canal, I think it was in November of 1917.
In this series I show you the stages of preparation and application for scribing and staining concrete floors. This is my second attempt at this craft, O.K. third try, our Harwich, (MA) barn was project one, the master bathroom in 71 Vista Concordia; and, now, the West Wing. The blue room, above, is in the process of protection from water based concrete stain application. We covered the lower 12" of the walls for this protection, sealed top and bottom to prevent leakage behind the protective membrane. We will leave this in-place until the floor is stained, scored, rinsed and the mildly acidic stain is neutralized; and, finally, sealed with a lacquer based concrete sealer.
We are using products from a company in Florida, under the name of Decosup, or decorative concrete supplies. Decosup's floor stains are a non-acidic solution which don't require HAZMAT (Hazardous Material) shipping. After all, shipping to this Island, 2,300 miles from Miami, FL, is expensive enough as it is for normal shipping rates.This shot of the south bedroom, sorry, the blue room, viewed down the Greenie Beanie (the name of the paint color) hallway, shows the application of the 1st stain coat, note the plastic film wall protection, taped to the wall top and bottom.
That black, cylindrical. & hosed aparatus in the center of the doorway is the stain applicator. I simply pour in the stain, pump up the pressure and pull the pistol grip handle to spray the liquid on the floor.
The vacuum cleaner I use for dust collection, and the floor jig for cutting straight lines is on the floor. The jig consists of two pieces of 1/4" masonite held parallel at the right dimension to allow for the concrete saw's footprint. This insures a straight and unwavering cut in the surface. The white cement, used to pour this layer, is extremely hard at this point, being fully cured now for several weeks. The handle of the saw pokes out of the closet at left of photo.
Wednesday, February 14, 2007
Everything but the.........
Debbie insisted I show the BEFORE and after shots of the scene, that is before she painted the edge around the countertop, where it meets the wall, nice, huh? The next shot down is the AFTER.
Tuesday, February 13, 2007
The Kitchen Sink
Labels: pouring the kitchen counter top
Thursday, February 08, 2007
The Master Bath Vanity
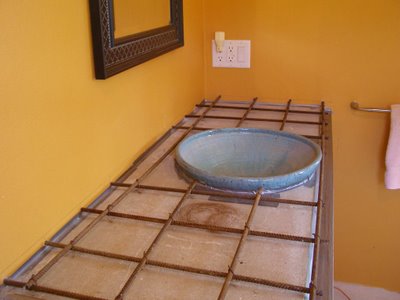